현대차가 1일 오후 유튜브를 통해 브랜드 첫 전용 전기차 아이오닉5의 탄생 과정을 담은 영상을 처음으로 공개했다. 아이오닉 5는 전기차 시대의 본격 도래를 알리는 친환경 차량으로 제품 성능과 디자인 뿐만 아니라 생산 방식도 기존의 자동차와 다른 혁신적인 자동화 공정을 거쳐 완성된다.
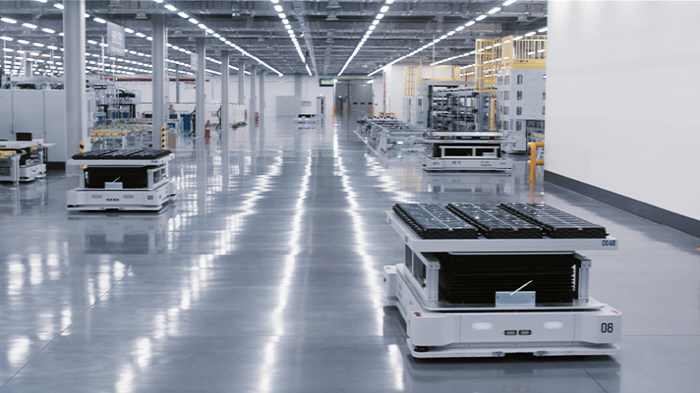
공장 내 지정 경로를 따라 이동하는 무인 운반 장치가 배터리 팩을 옮기고 있다. 무선통신, 추돌방지 센서들을 통해 주변 장애물을 피해 목적지까지 최적의 경로로 자율 주행한다. [사진 제공 = 현대자동차]
이번에 공개된 영상에서는 아이오닉5의 핵심 요소라 할 수 있는 ▲ ICCU(Integrated Charging Control Unit) ▲ PE시스템(Power Electric System) ▲ 배터리 팩 제작과정 등 전용 전기차에만 적용되는 부품들의 제조 공정을 확인할 수 있다. 또한 작업 환경의 안전성과 품질 경쟁력 향상을 위해 도입된 ▲ 무인 운반 장치(Automated Guided Vehicle·AGV) ▲ 전장집중검사를 진행하는 과정도 볼 수 있다.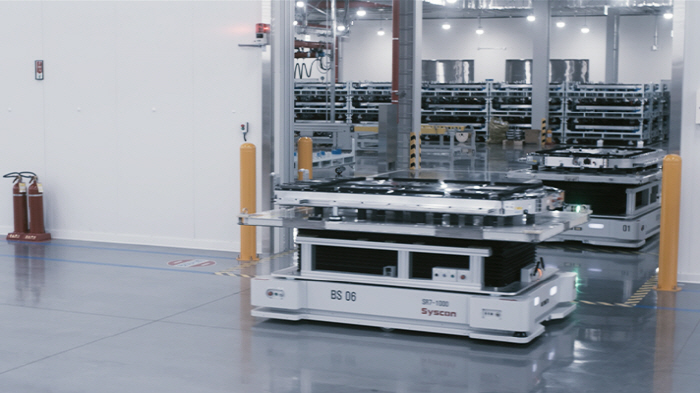
공장 내 지정 경로를 따라 이동하는 무인 운반 장치가 배터리 팩을 옮기고 있다. 무선통신, 추돌방지 센서들을 통해 주변 장애물을 피해 목적지까지 최적의 경로로 자율 주행한다. [사진 제공 = 현대자동차]
영상에서 첫번째로 등장하는 ICCU는 전기차에 탑재된 고전압 배터리와 보조배터리 모두 충전이 가능하도록 현대차그룹이 새롭게 개발한 통합 충전 시스템이다. ICCU는 개별 부품의 이동, 조립, 용접은 물론, 완성품의 이동까지 모든 제조 공정이 자동으로 이뤄진다. 청정한 작업환경과 정밀함이 요구되는 전력 공급 장치 특성상 생산 라인은 클린룸 내에 설치돼 있다.![아이오닉5의 다양한 전장 시스템 기능들이 제대로 작동하는지 전장 집중검사를 실시하고 있다. [사진 제공 = 현대자동차]](https://img.mbn.co.kr/filewww/news/other/2021/07/01/170025000011.jpg)
아이오닉5의 다양한 전장 시스템 기능들이 제대로 작동하는지 전장 집중검사를 실시하고 있다. [사진 제공 = 현대자동차]
두번째로 등장하는 PE 시스템은 내연기관 자동차의 파워트레인을 대체하는 전기차 구동 장치다. 아이오닉5의 PE 시스템에 적용되는 구동 모터는 고난이도 공법인 '헤어핀 권선' 방식이 적용된다. 헤어핀 권선 기술은 말 그대로 머리핀(헤어핀)의 형상을 닮은, 직사각형의 단면을 가진 코일을 활용한 구조를 뜻한다. 헤어핀 권선과 코일이 감겨 있는 고정자를 조립하는 로봇 공정을 마치고 나면 작업자들의 정교한 연결 작업이 더해져 복잡한 내부 구조를 마무리한다.![전장 집중 검사를 마친 아이오닉 5를 대상으로 마지막 공정인 의장 라인에서 숙련된 작업자들이 최종 품질 확인 절차를 실시하고 있다. [사진 제공 = 현대자동차]](https://img.mbn.co.kr/filewww/news/other/2021/07/01/008280001001.jpg)
전장 집중 검사를 마친 아이오닉 5를 대상으로 마지막 공정인 의장 라인에서 숙련된 작업자들이 최종 품질 확인 절차를 실시하고 있다. [사진 제공 = 현대자동차]
그 다음으로 등장하는 배터리 팩 조립 과정은 셀에 다공성 재질의 패드를 부착하는 공정부터 시작한다. 작업자가 작업판에 폴리우레탄(PU) 패드를 적재하면 자동화 설비가 낱장의 패드를 진공 흡착한 후 양면 필름을 벗겨내고 이후 필름이 벗겨진 패드를 셀에 다시 부착해 높은 압력을 가해 완전히 점착시킨다. PU 패드가 부착된 셀은 카메라를 이용한 자동화 시각 검사인 비전 시스템을 통해 정확한 위치에 부착됐는지, 필름은 정상적으로 벗겨졌는지 등을 확인한 후 다음 공정으로 이동한다.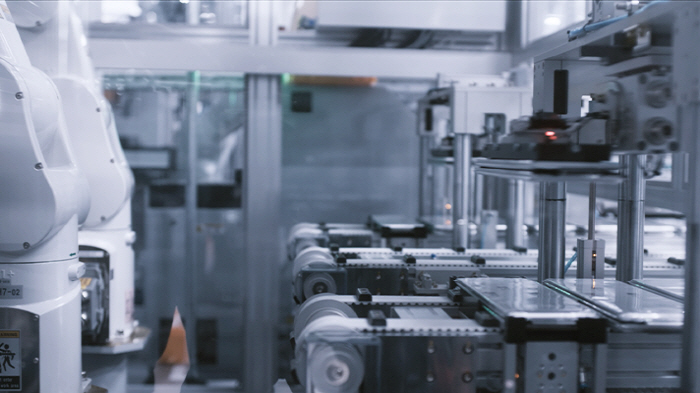
6축 다관절 로봇이 컨베이어에 12개의 배터리 셀을 차곡차곡 쌓아 1개의 모듈로 만들고 있다. 개별 셀의 위치가 배터리 품질에 결정적인 영향을 미치기 때문에 0.2mm 오차 범위 내에서 정확한 위치에 셀을 옮긴다. [사진 제공 = 현대자동차]
이어지는 공정은 6축 다관절 로봇이 컨베이어에 셀을 차곡차곡 쌓아 12개를 1개의 모듈로 만드는 과정이다. 개별 셀의 위치가 배터리 품질에 결정적인 영향을 미치기 때문에 0.2mm 편차 범위 내에서 정확한 위치에 셀을 옮긴다. 손상되기 쉬운 셀의 특성을 고려해 모든 설비 동작은 적절한 가압을 유지하며 진행된다. 아이오닉 5에 탑재되는 배터리 모듈은 현대차그룹의 전기차 전용 플랫폼인 E-GMP를 위해 새롭게 개발된 것으로, 에너지 밀도를 크게 높여 부피를 최소화한 점이 특징이다. 영상 속 배터리 모듈의 크기가 매우 콤팩트한 것이 바로 이 때문이다.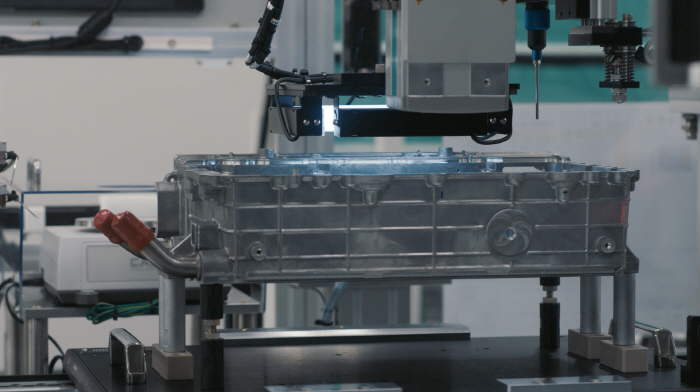
전기차에 탑재된 고전압 배터리와 보조배터리 모두 충전이 가능하도록 현대자동차그룹이 새롭게 개발한 통합 충전 시스템 `ICCU`가 클린룸에서 자동화 공정을 통해 제작되고 있다. [사진 제공 = 현대자동차]
완성된 배터리 팩은 무인 운반 장치(AGV)에 실려 정해진 장소를 향해 이동한다. 무인 운반 장치는 미리 저장된 지도 상의 경로를 따라 이동하며 무선통신·추돌방지 센서들을 통해 주변 장애물을 피해 목적지까지 최적의 경로로 자율 주행하며 생산성을 높이는 시스템이다. 작업자가 직접 무거운 부품을 끌고 다니지 않아도 되기 때문에 작업 환경과 안전성이 개선된 것이 장점이다. 뿐만 아니라 실시간 제어를 통해 정확한 시간과 장소에 맞춰 부품을 옮길 수 있고, 무인 운반 장치의 이동 동선 최소화로 공장의 규모를 최적화하는 한편 부품 품질 관리도 용이하다.![내연기관 자동차의 파워트레인을 대체하는 전기차 구동장치 PE시스템이 고난이도 공법인 헤어핀 권선 방식으로 제작되고 있다. [사진 제공 = 현대자동차]](081200701211.jpg)
내연기관 자동차의 파워트레인을 대체하는 전기차 구동장치 PE시스템이 고난이도 공법인 헤어핀 권선 방식으로 제작되고 있다. [사진 제공 = 현대자동차]
이처럼 현대차가 지향하는 스마트 팩토리는 인공지능(AI)과 로봇 기술 등 혁신적인 자동화 방식을 적용한 것이 특징이다. 무인 운반 장치에 실려 지정된 장소로 옮겨진 배터리 팩은 ICCU와 PE 시스템, 그리고 앞뒤 서스펜션, 구동계 등과 만나 E-GMP 플랫폼으로 완성된다.![내연기관 자동차의 파워트레인을 대체하는 전기차 구동장치 PE시스템이 고난이도 공법인 헤어핀 권선 방식으로 제작되고 있다. [사진 제공 = 현대자동차]](https://img.mbn.co.kr/filewww/news/other/2021/07/01/080800120002.jpg)
내연기관 자동차의 파워트레인을 대체하는 전기차 구동장치 PE시스템이 고난이도 공법인 헤어핀 권선 방식으로 제작되고 있다. [사진 제공 = 현대자동차]
한편 E-GMP 플랫폼이 순차적으로 완성되는 사이 다른 한쪽에서는 아이오닉 5의 차체가 제작된다. 차체를 구성하는 패널과 뼈대를 조립해 외형을 완성하는 차체 라인에 이어 색상을 입히는 도장 라인까지 작업 공정에 따라 산업용 로봇들이 절도 있는 작동과 유연하고 섬세한 움직임으로 작업을 마치고 나면 아이오닉 5가 외형을 갖추게 된다.다양한 전장 시스템이 적용된 아이오닉 5는 각종 기능이 제대로 작동하는지를 점검하는 과정도 거친다. 컴퓨터가 설정된 데이터를 입력해 해당 데이터에 따라 카메라와 레이더 등 각종 센서가 제대로 작동하는지 빠르고 정확하게 검사를 진행하는 것이다.
![로봇들이 일사불란하게 움직이며 전기차의 심장이라 할 수 있는 배터리 팩 조립을 위해 배터리 셀을 조립하고 있다. [사진 제공 = 현대자동차]](https://img.mbn.co.kr/filewww/news/other/2021/07/01/101501201210.jpg)
로봇들이 일사불란하게 움직이며 전기차의 심장이라 할 수 있는 배터리 팩 조립을 위해 배터리 셀을 조립하고 있다. [사진 제공 = 현대자동차]
아이오닉 5는 검사 시스템을 통해 ▲ 서라운드 뷰 모니터(Surround View Monitor·SVM) ▲ 전방 주행 정보 표시 장치(Head Up Display·HUD) ▲ 전측방 레이더 (Front Corner Radar) ▲ 디지털 사이드미러(Digital Side Mirror) 등 기능을 확인하고 보정한다. 첨단 전자 장비와 각종 시스템의 정상적인 작동 여부를 확인하는 전장 검사 시스템은 품질의 편차를 줄이고 신뢰성을 높일 수 있도록 돕는 것이 특징이다.전장 집중 검사를 마친 아이오닉 5는 마지막 공정인 의장라인에서 숙련된 작업자들의 눈썰미와 손길로 작업을 마치고 최종 품질 확인절차까지 거치고 나면 드디어 아이오닉 5 생산의 대단원을 마무리하게 된다.
현대차 관계자는 "고객들의 뜨거운 관심을 받고 있는 아이오닉 5 제작 과정에 대해 다양한 이해관계자와 소통하고자 해당 영상을 제작했다"며 "인공지능과 빅데이터를 활용한 스마트 팩토리 운영은 소비자를 위한 최상의 제품을 만드는 데 목적이 있는 만큼 정확한 데이터를 기반으로 제품 생산의 정확성과 효율성을 높여갈 것"이라고 밝혔다. [박윤구 기자]
[ⓒ 매일경제 & mk.co.kr, 무단전재 및 재배포 금지]
기사에 대해 의견을 남겨주세요.